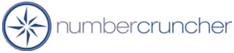
The All Orders is a simple-to-use QuickBooks inventory add-on for production and order management. It is designed to augment the tools available in QuickBooks by adding features such as multiple warehouse, lot and serial # tracking, routing and more. The table below summarizes the key differences between All Orders by NumberCruncher and QuickBooks Premier or Enterprise. Additional explanation is provided below the table.
Feature | All Orders | QuickBooks |
---|---|---|
Items / Inventory Control | ||
Assemblies / BoMs | Yes | Yes |
Jobs | Yes | No |
Configuration | Yes | No |
Routing / Operations | Yes | No |
Min/Max/Reorder | Yes | No |
Multiple Vendors | Yes | No |
Pricing Levels | customer, item, company, volume, item group | customer, item |
Units of measure | Yes | 2007 |
Item categories (groups) | Yes | No |
Item replacement / up sell | Yes | No |
Lots and Serial # | Yes | Ent. 2012 with Adv. Inventory
See why All Orders is better! |
Multiple warehouses | Yes | Ent. 2011 with Adv. Inventory |
Bins | Yes | No |
Bar code printing & scanning | Yes | No |
Work in Process | Yes | No |
Multilevel BoMs with cost roll-up | Yes | No |
Changeable components per work order | Yes | 2010 |
Single user mode to adjust inventory | No | Yes |
Order Processing | ||
Sales Order | Yes | Yes |
Quotes | Yes | Yes |
Release dates | Yes | No |
Item Configuration | Yes | No |
Ship-to-addresses | Yes | Yes |
Payment on SO | Yes | No |
Customer info page | Yes | Yes |
Ship complete | Yes | No |
Auto fill | Yes | No |
Ship negative | Preference | Yes |
SO to PO | Yes | Yes |
SO to WO | Yes | No |
Drop Ship | Yes | Yes |
Batch Filling | Yes | No |
Back order reports | Yes | No |
Last products ordered | Yes | No |
PO ETA | Yes | No |
Stock by Location | Yes | Ent. 2011 with Adv. Inventory |
Order duplication | Yes | Yes |
Sales rep filtering | Yes | No |
Foreign currency | Yes | Yes |
Sales taxes | Yes | Yes |
Customer Part #s | Yes | No |
Yes | Yes | |
Shipping | ||
Scan-out | Yes | No |
Serial / Lot #s | Yes | Ent. 2012 with Adv. Inventory |
Bin Picking | Yes | No |
Auto-allocate | Yes | No |
Count packages | Yes | No |
Count weight | Yes | No |
UPS World Ship | Yes | No |
UPS / Fed Ex Internet | Yes | Yes |
Sales Tax | Yes | Yes |
Payment (cash sale) | Yes | Yes |
Foreign currency | Yes | No |
Shipping labels | Yes | Yes |
Product labels | Yes | No |
Batch shipping | Yes | No |
Auto-return | Yes | No |
Purchasing | ||
Purchase Orders | Yes | Yes |
Release dates | Yes | No |
Order approval | Yes | No |
Batch creation | Yes | No |
Filter items by vendor | Yes | No |
Lead times | Yes | No |
Min order and order increment | Yes | No |
Vendor part #s | Yes | No |
Manufacturer's part #s | Yes | No |
Drop ship | Yes | Yes |
Yes | Yes | |
Reorder Points | Dynamic | Static |
Min/Max | Yes | No |
Receiving | ||
Scan in | Yes | No |
Serial / Lots # | Yes | Ent. 2012 with Adv. Inventory |
Bins | Yes | No |
Product Labels | Yes | No |
Charges | Yes | No |
Production | ||
Bill of Materials | Yes | Yes |
Routing | Yes | No |
Work Orders | Yes | No |
Disassemblies | Yes | No |
Auto pick | Yes | No |
WO to PO | Yes | No |
WO to WO | Yes | No |
Item Assembly is a type of item in QuickBooks Premier and Enterprise. The Item Assembly represents finished goods items. So if you already have your items set up as inventory parts, you will have to re-enter them. Within the Item Assembly you specify the components which are only inventory items and their quantities. Service items, other charges, and non-inventory are not allowed. To create an Item Assembly, you go to an entry screen that looks like an “Inventory Adjustment” and you specify how many you want to make. QuickBooks will tell you how much components you need and how many finished goods you can make based on components “On Hand.” You cannot change the components on each build; in order to do that you need to change the original assembly item. QuickBooks Assemblies do not have routing.
By contrast, All Orders uses a Bill of materials (BoM) instead of Item Assembly. It allows you to specify which of your existing Inventory Parts are finished goods and which are components. You also specify an item's “unit of measure.” BoMs work with your existing inventory parts, non-inventory parts, service and other charge items.
You can immediately determine the costing and margin information because All Orders sums the cost of all of its components for you using either the average costs or purchase costs.
With All Orders you can have sub-assemblies with full cost roll-up. If you change the cost or quantities in a bill of material of one of the sub-assemblies, it will immediately be reflected in the costs of the items that depend on it.
A sales order tells you what you have to ship, whereas a work order tells you what you need to produce. A work order in All Orders is derived from the sales order template which simply shows the items that were ordered.
The work order is a management document that tells the user three key pieces of information:
A sales order does not show you anything about production status or component status.
All Orders provides a number of tools that help you efficiently manage inventory. None of these tools are available in QuickBooks. These include locations and bins, lots and serial # tracking and units of measure. In addition, All Orders allows you to do the following:
All Orders sales orders have a number of additional features not found in QuickBooks Premier or Enterprise. You can ship to multiple addresses on the same sales orders. Additionally you can ship multiple sales orders on the same packing slip. All Orders information provides back order and “can ship” information, as well as complete inventory status and costing for each product.
You can create work orders and purchases orders for short stock directly from the sales order, that way you can track dependency information.
An All Orders sales order turns into a shipping doc/packing slip. You can also track an order’s ship dates and whether an invoice has been created for the shipment.
Download a Free Trial version now!
Or call to speak with a NumberCruncher Solutions Consultant at: